RV Trailer Decking
2018/06/17 08:00 Filed in: RV Trailer | Welding
Adding some strength to the trailer frame.
Several pieces of angle were cut to be welded on to the frame to allow the attachment of the deck and wood frame (for the cabin).
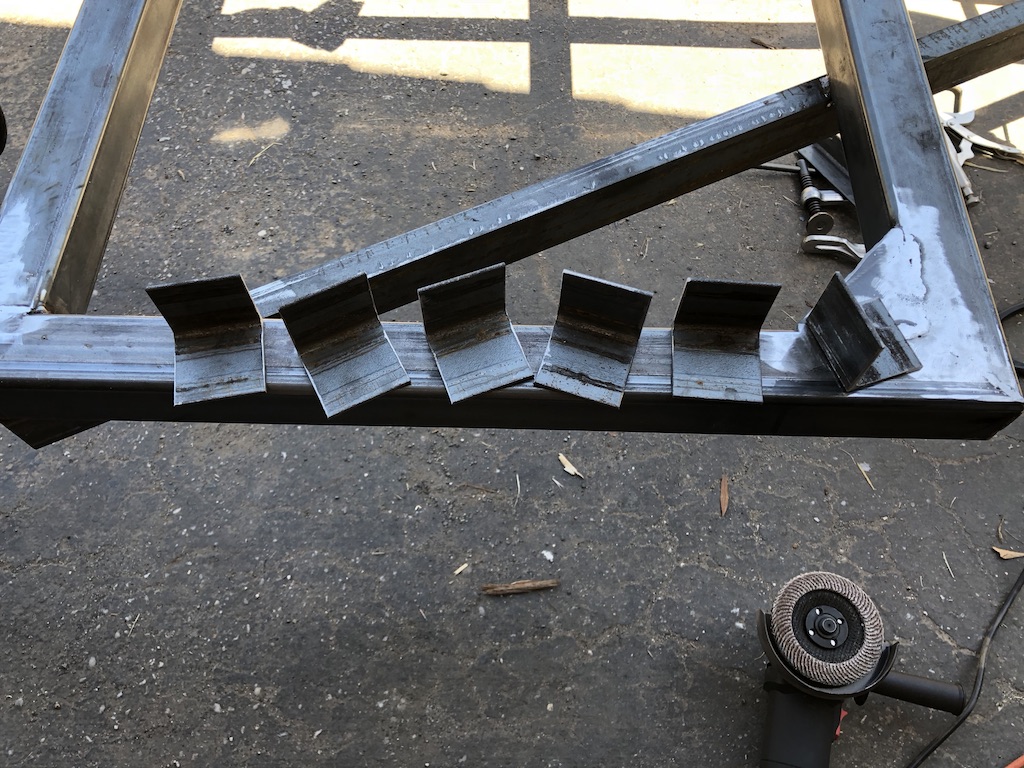
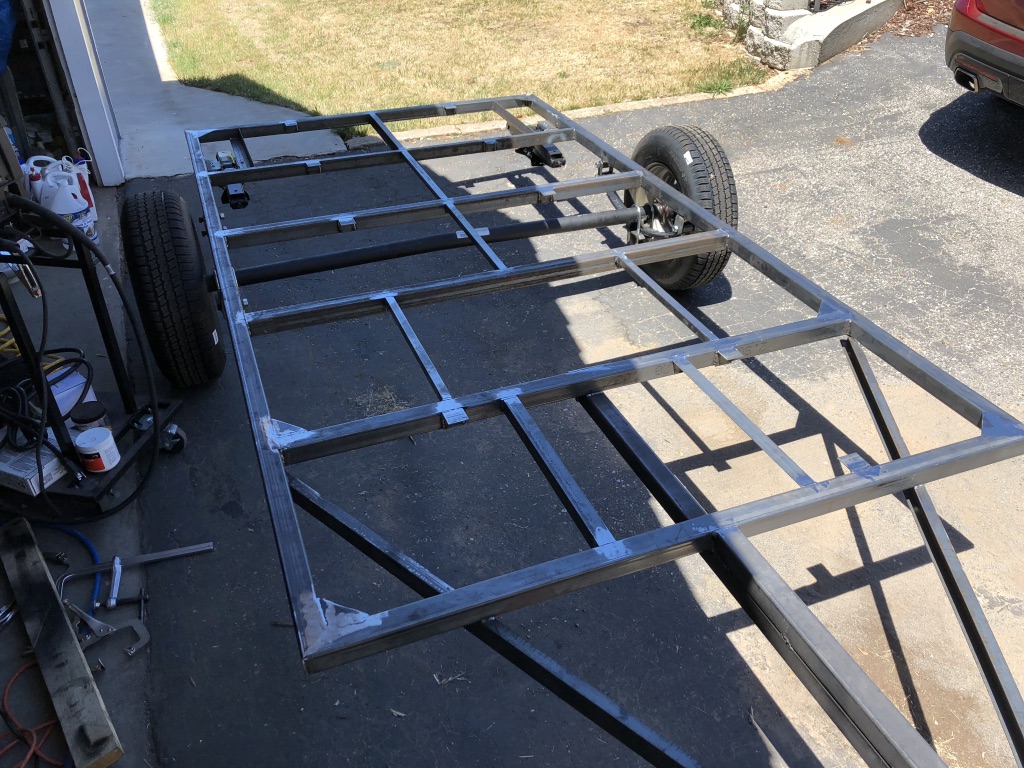
Rough fitting test of the first piece of 20awg steel sheet:
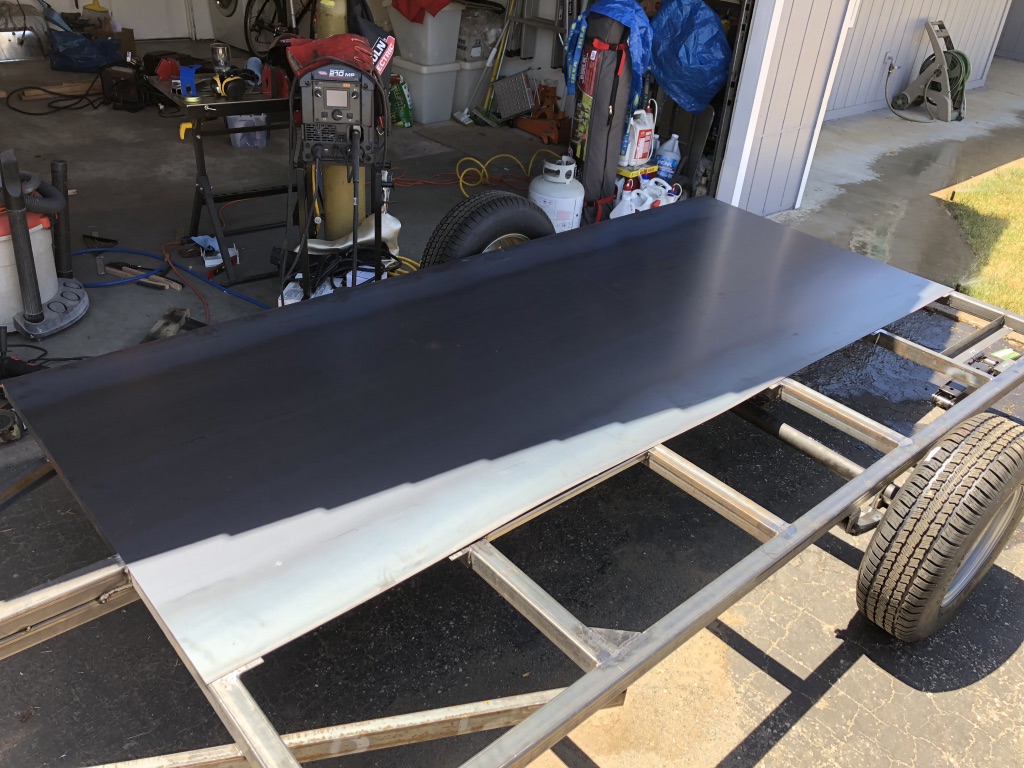
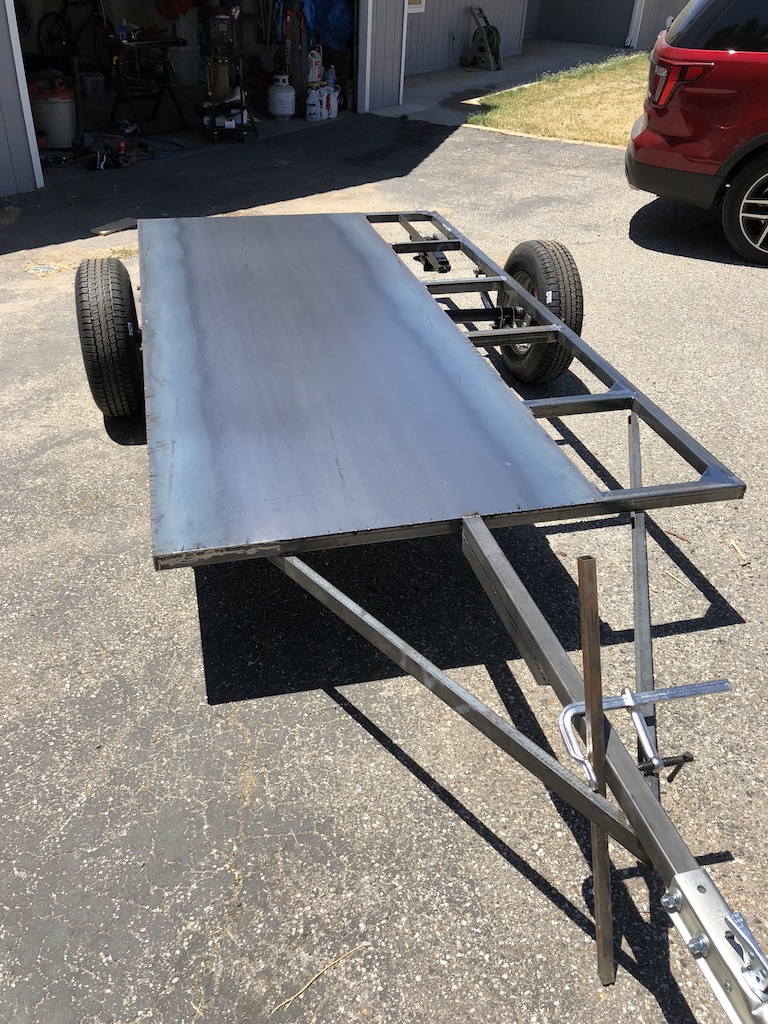
Tacked in place:
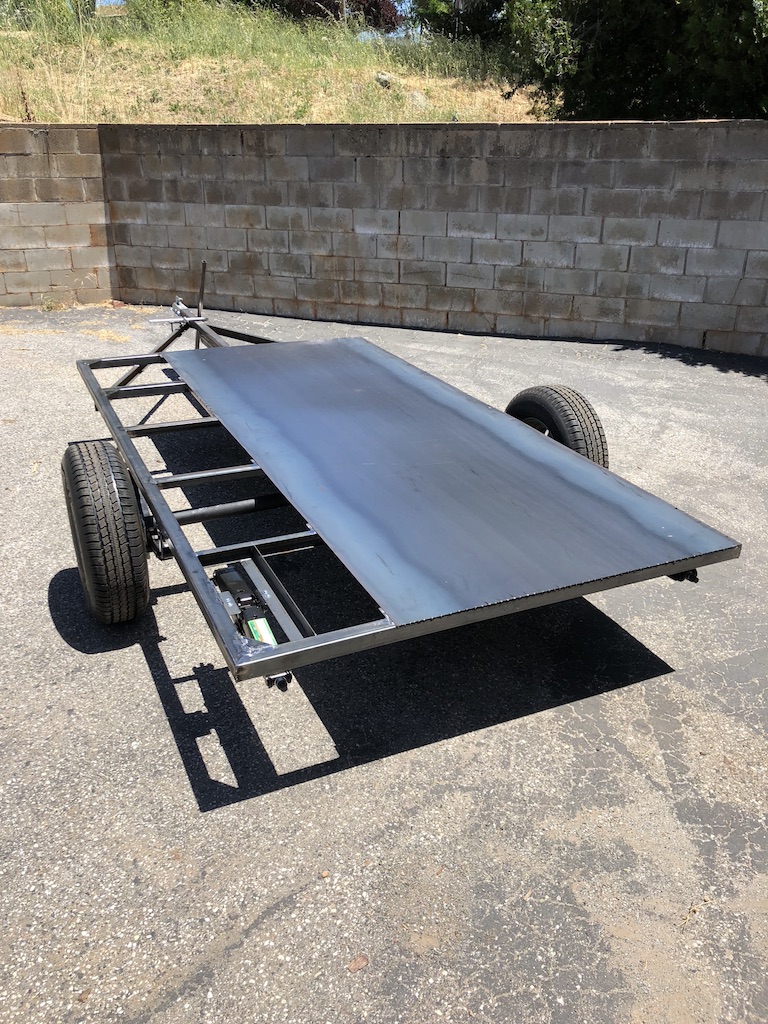
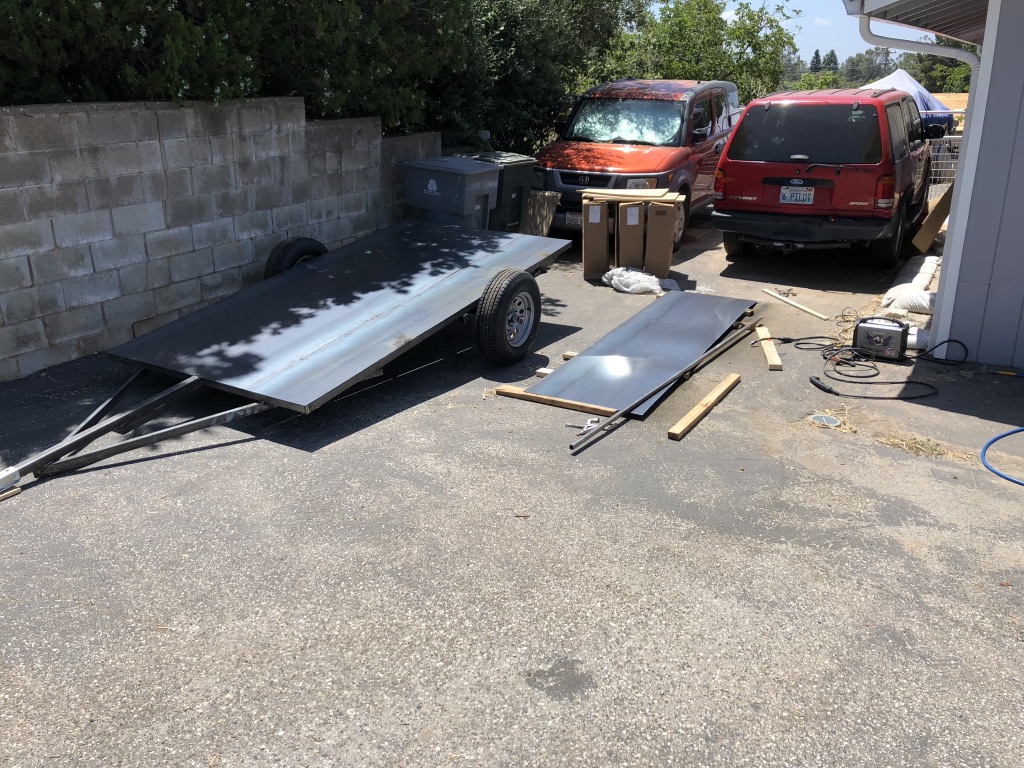
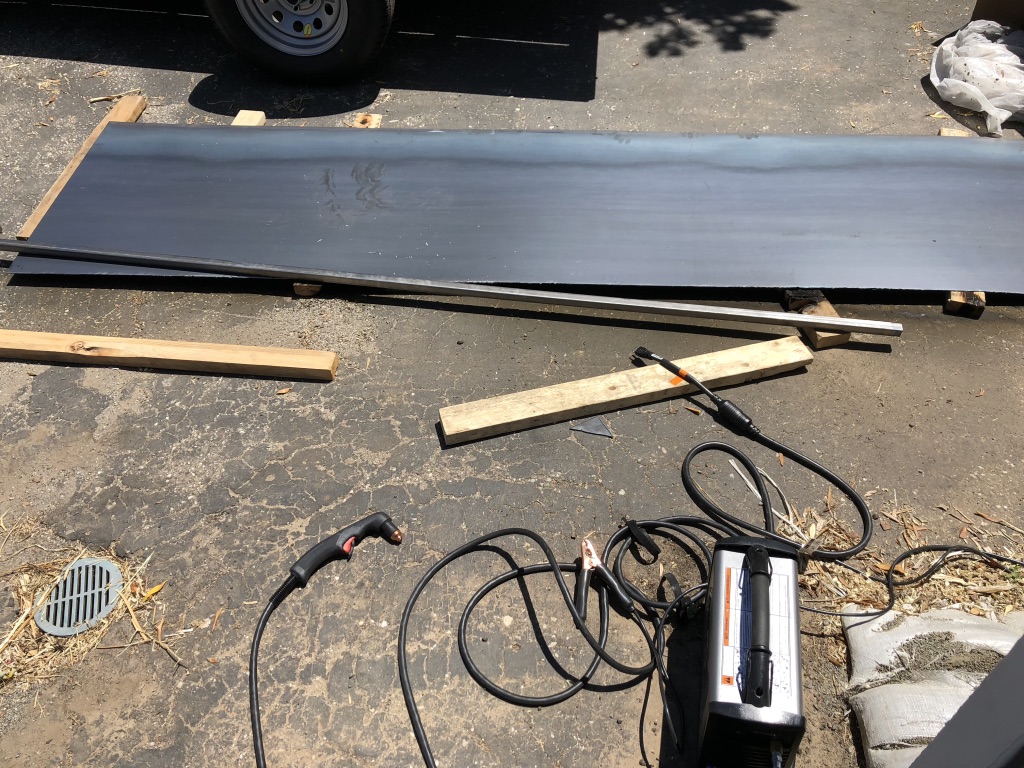
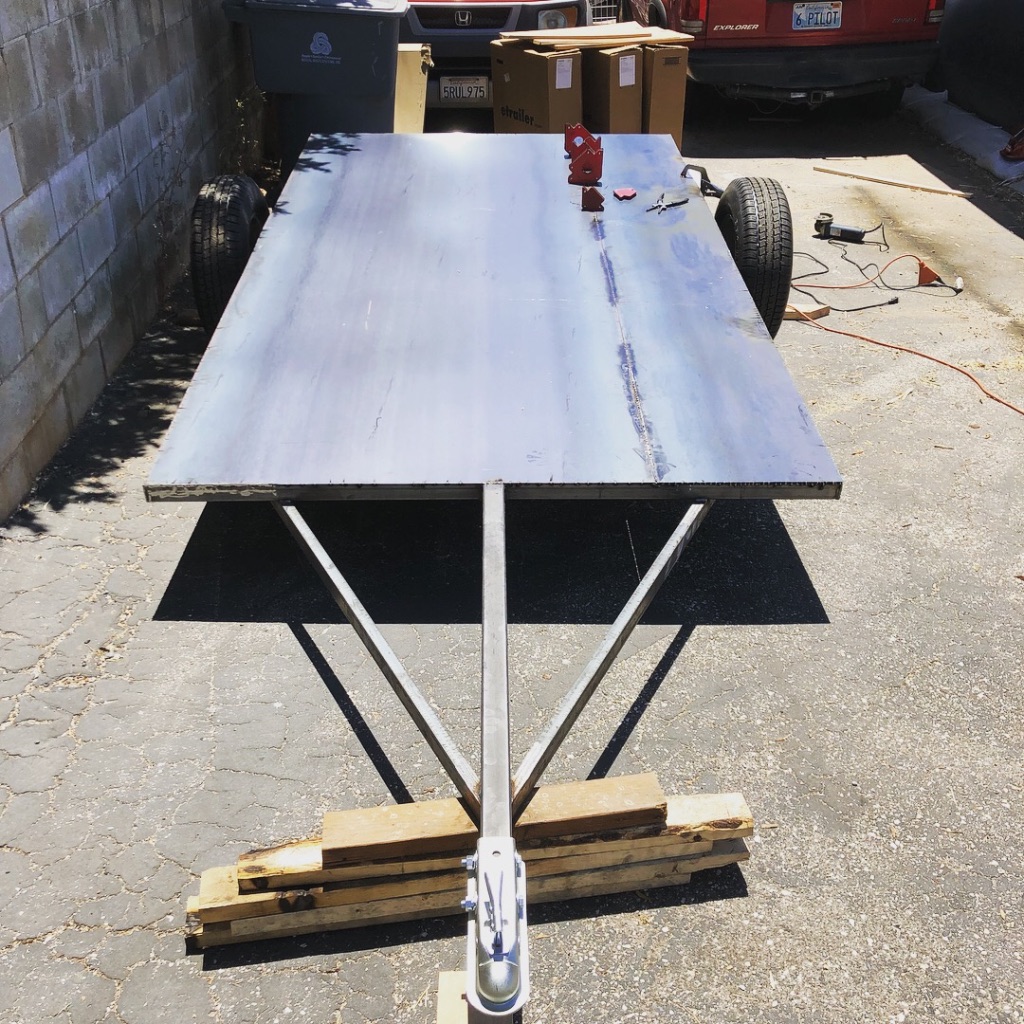
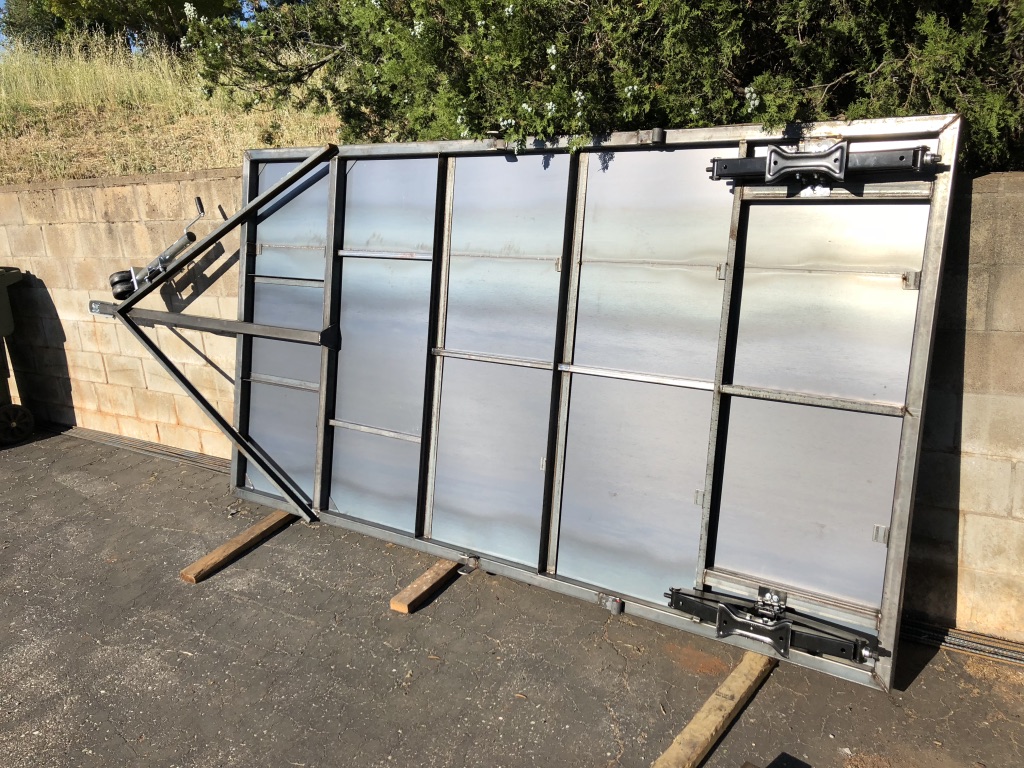
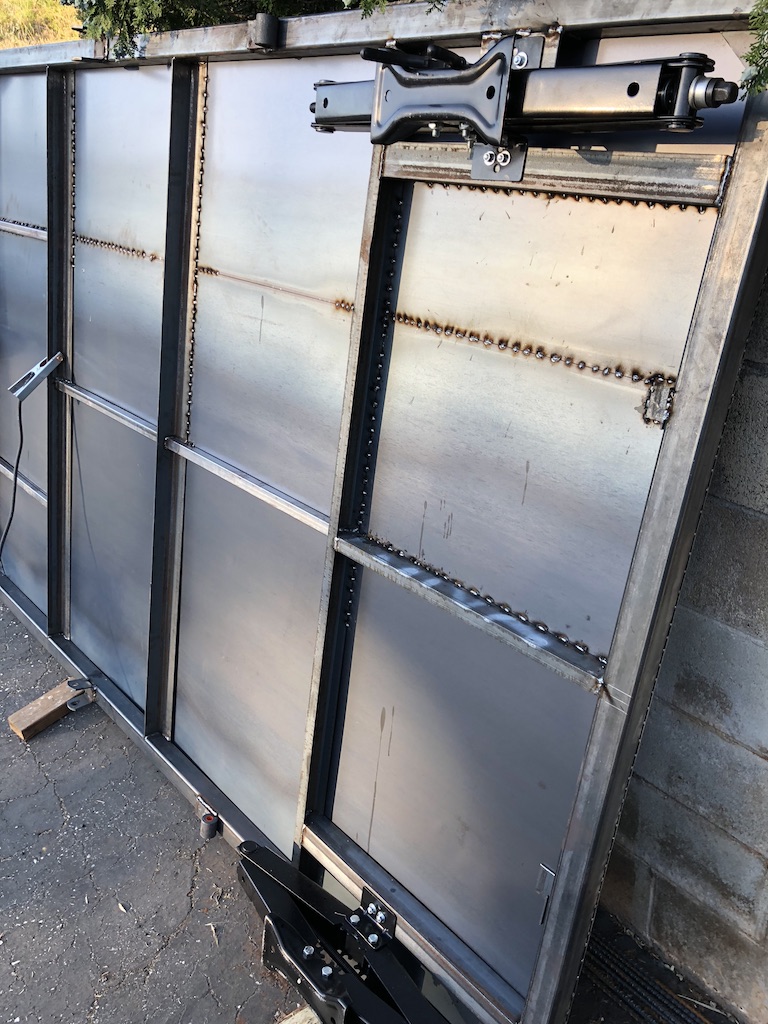
Several pieces of angle were cut to be welded on to the frame to allow the attachment of the deck and wood frame (for the cabin).
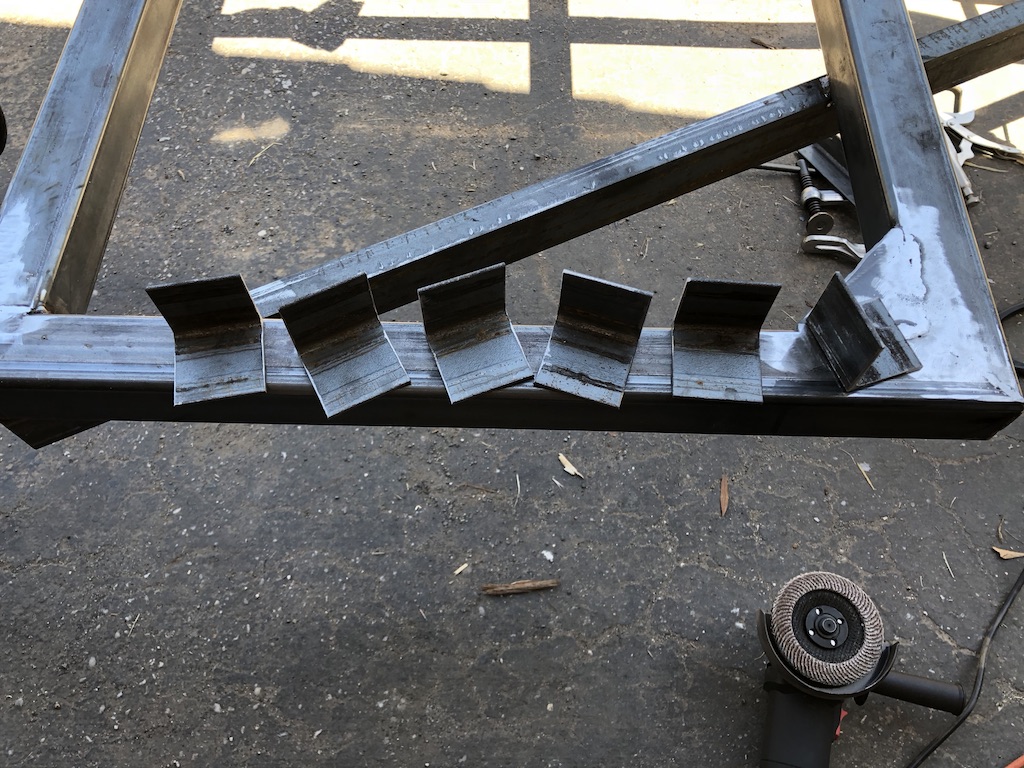
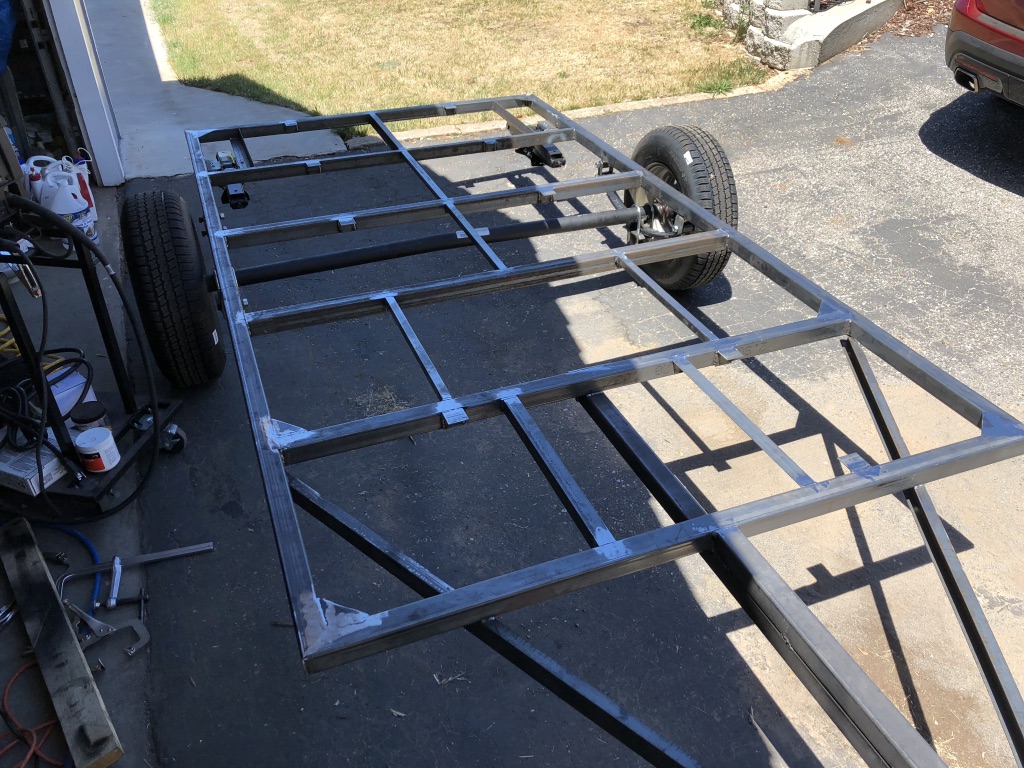
Rough fitting test of the first piece of 20awg steel sheet:
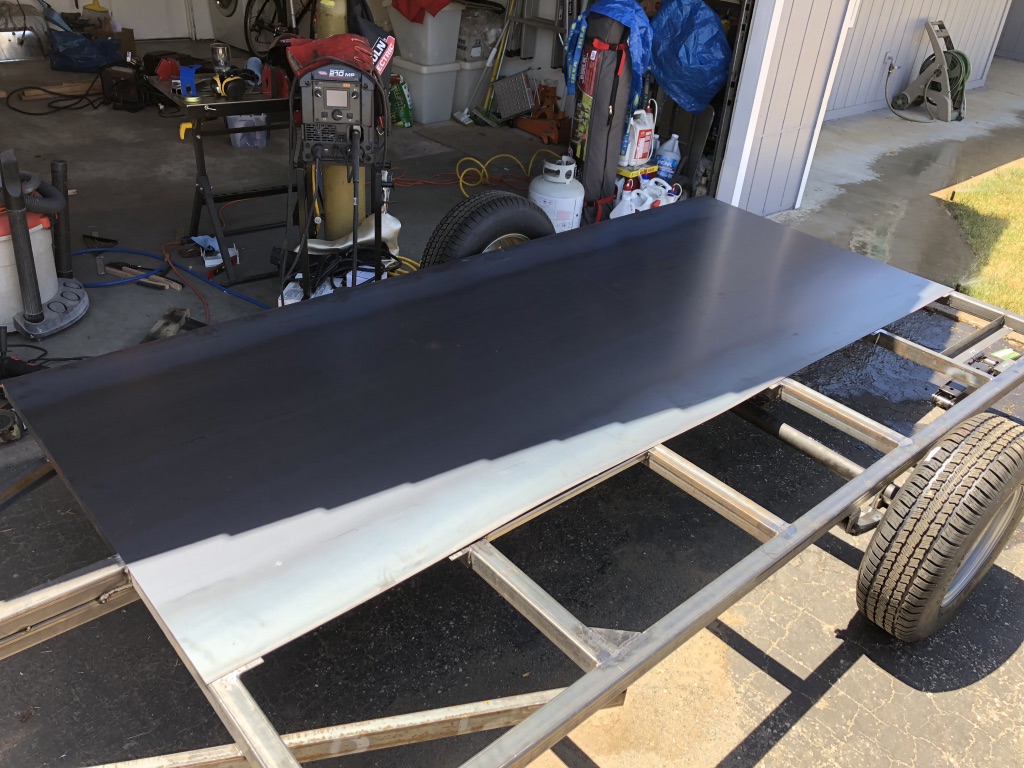
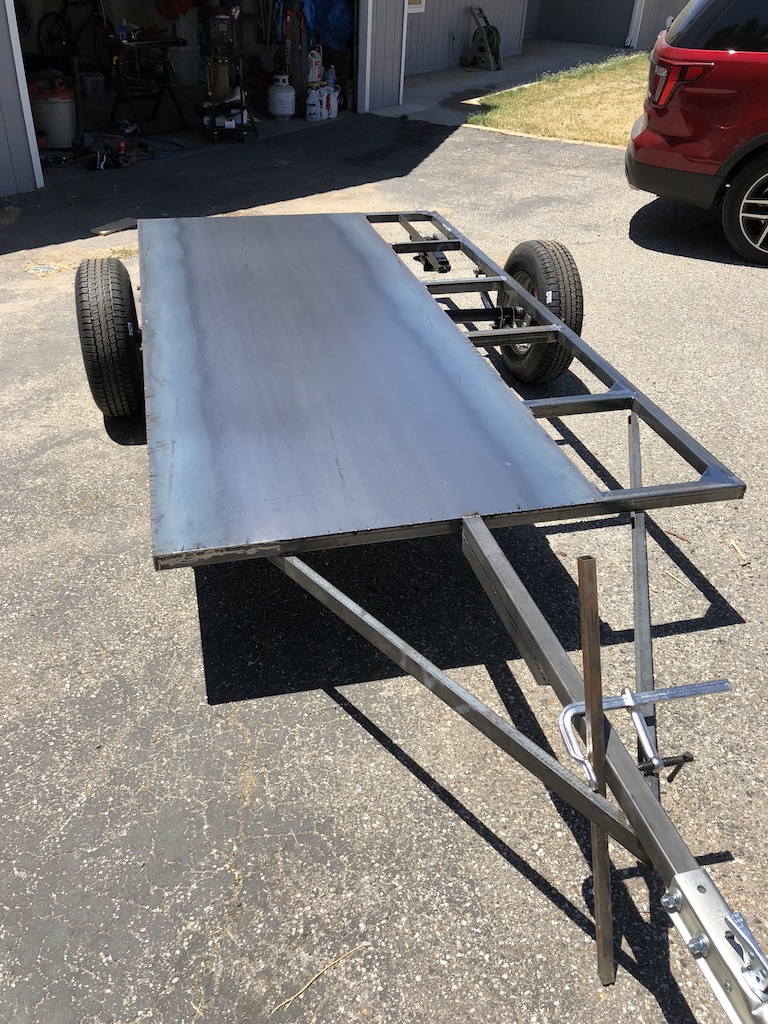
Tacked in place:
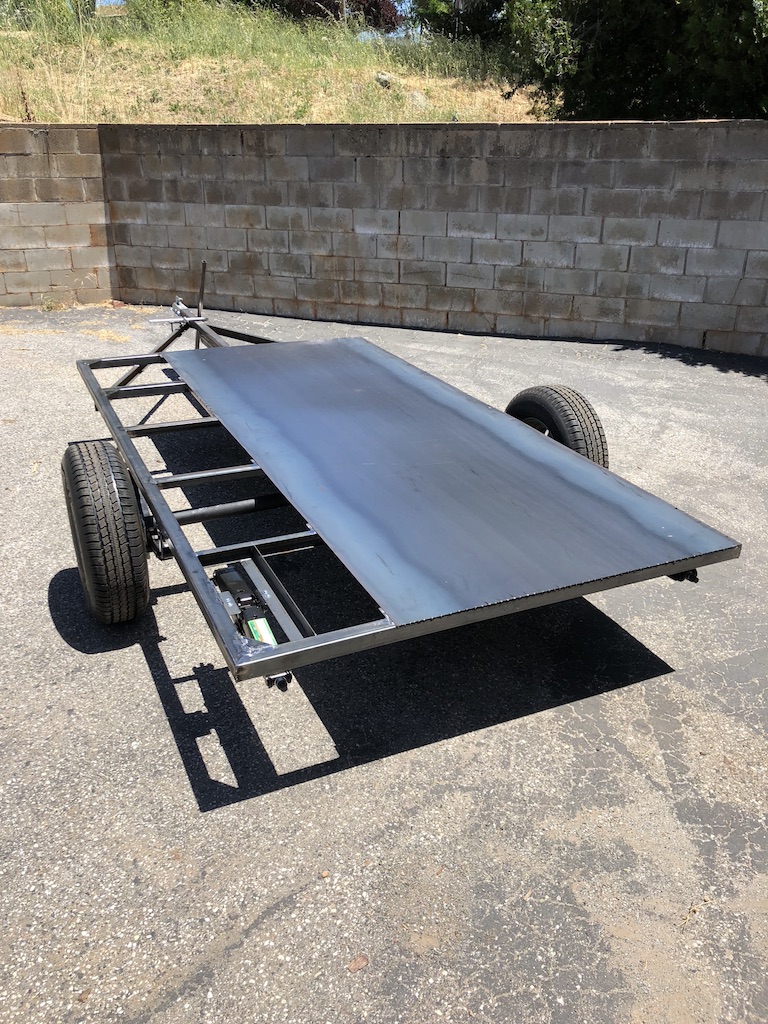
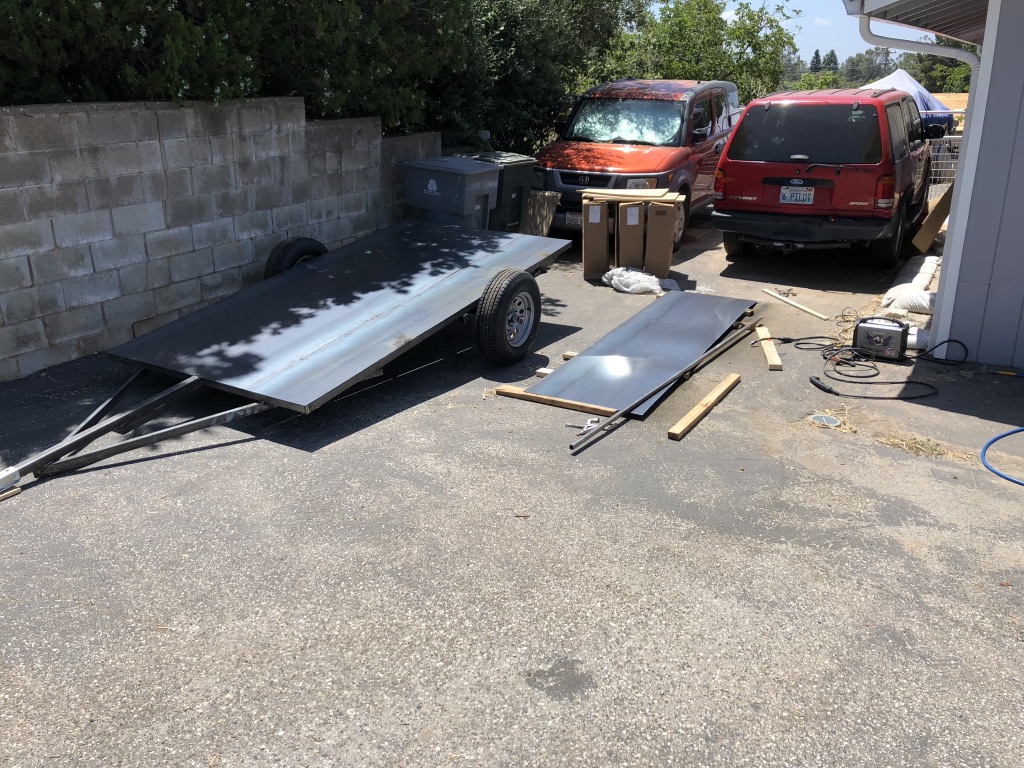
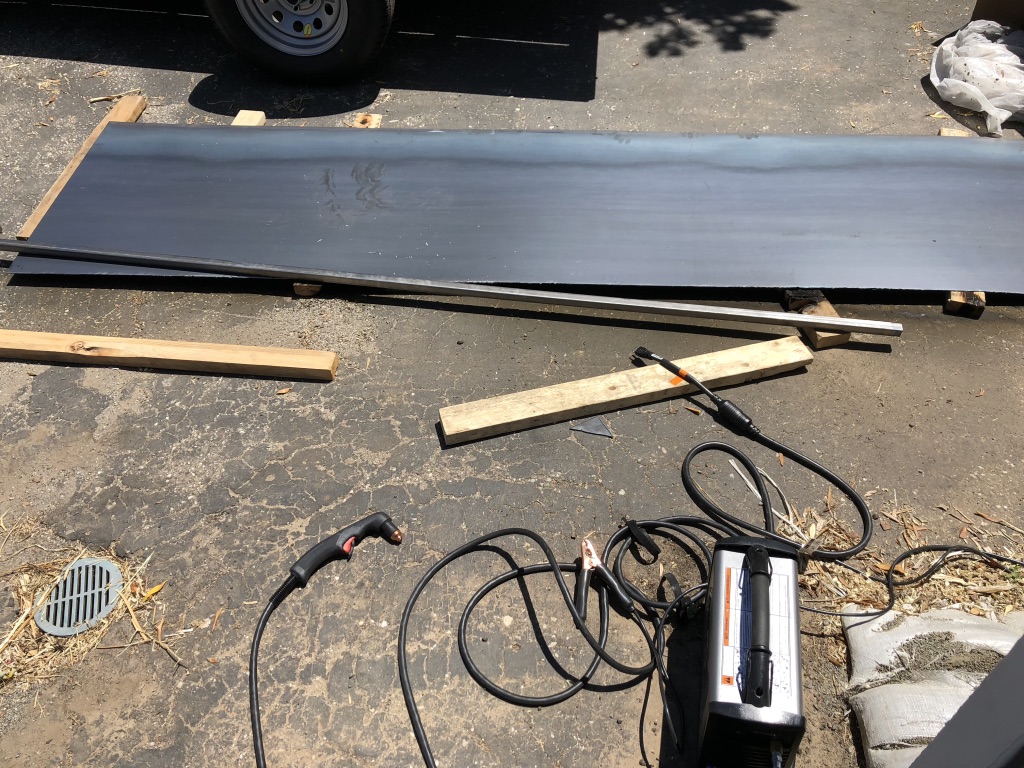
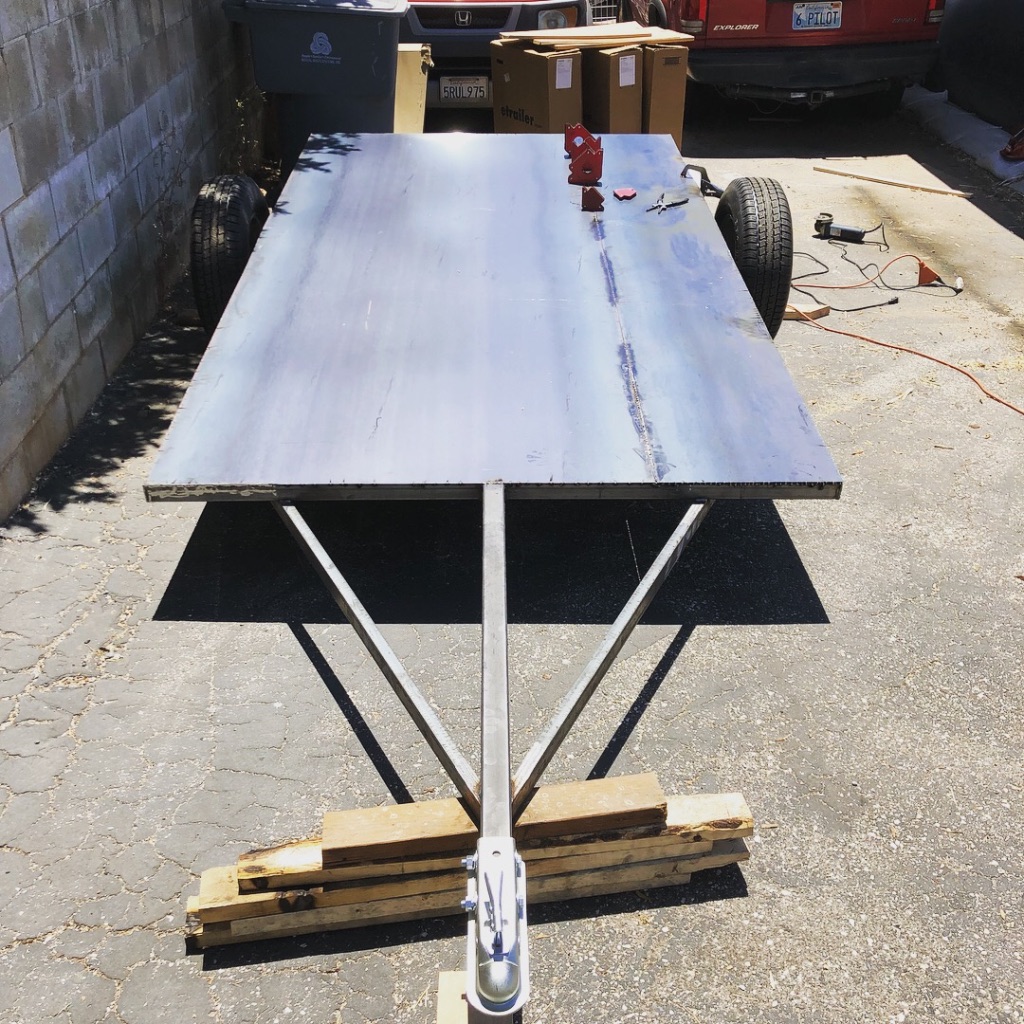
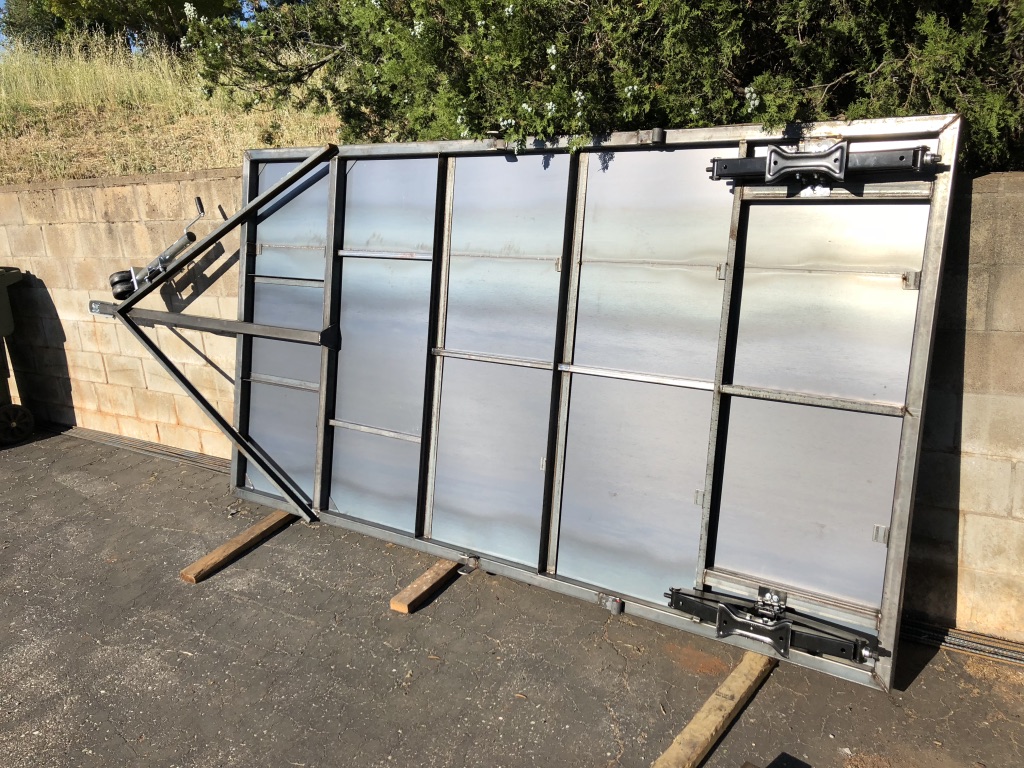
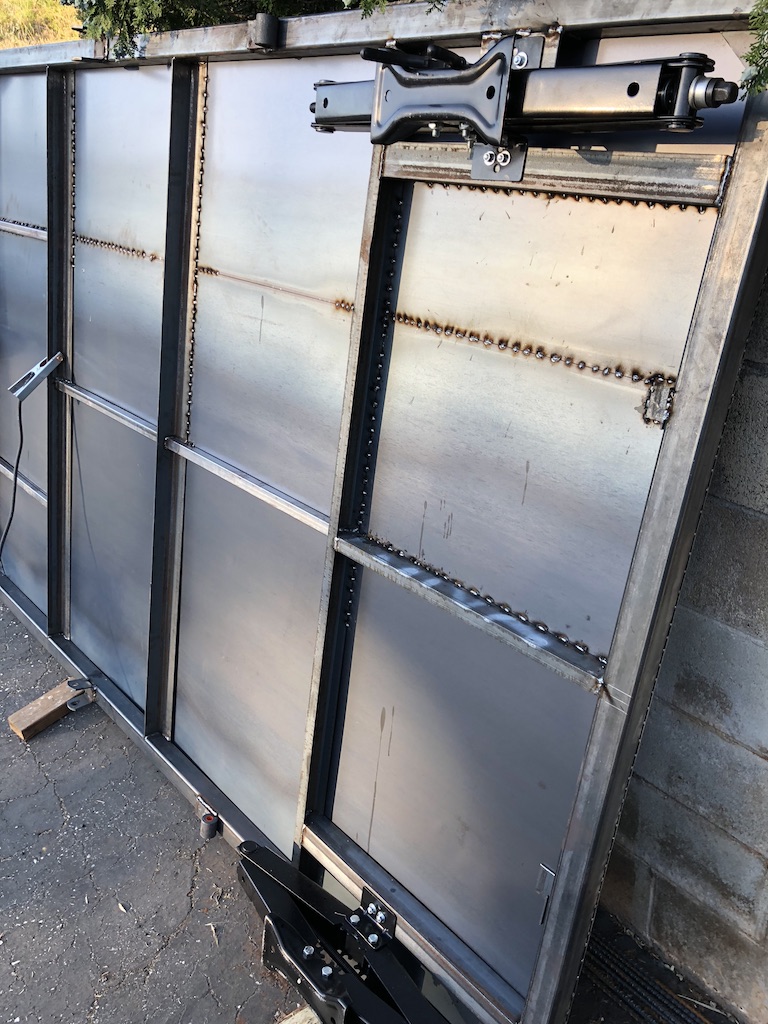
RV Trailer leveling jacks
2018/06/10 16:32 Filed in: RV Trailer | Welding
RV Trailer leveling jacksAdding leveling jacks to the RV trailer frame.
These are simple scissor jacks that were procured from Harbor Freight.
2.5t scissor jack: https://www.harborfreight.com/2-1-2-half-ton-trailer-stabilizer-jack-96406.html
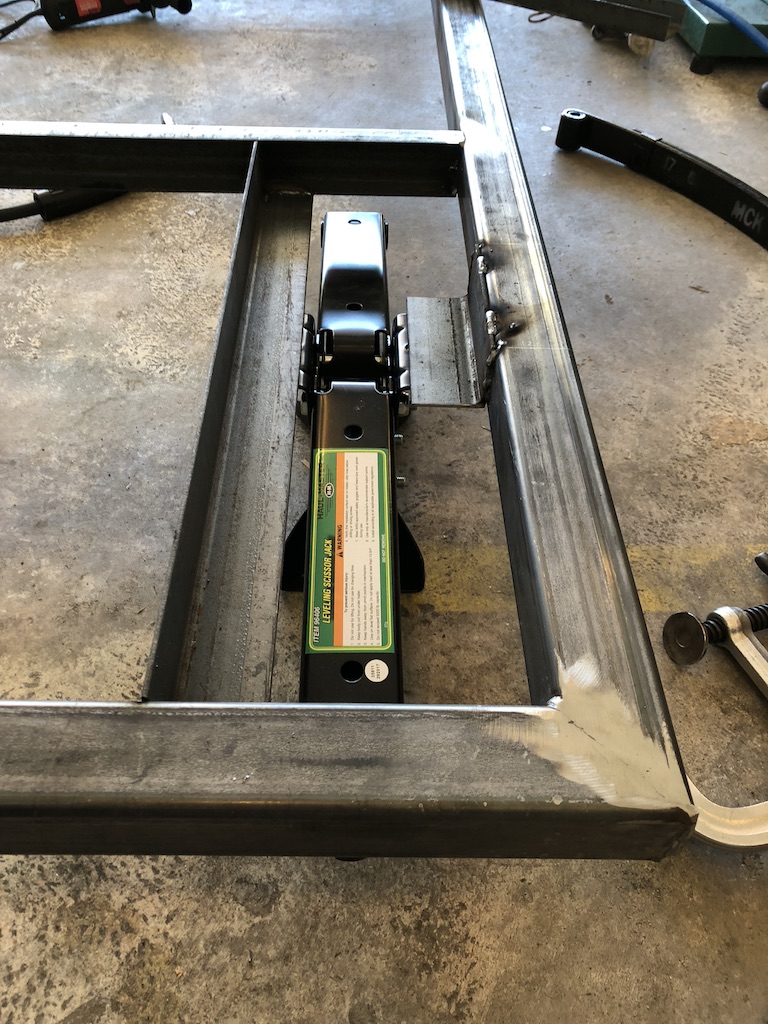
Using some 2″ angle, a suitable attachment was made for the jack.
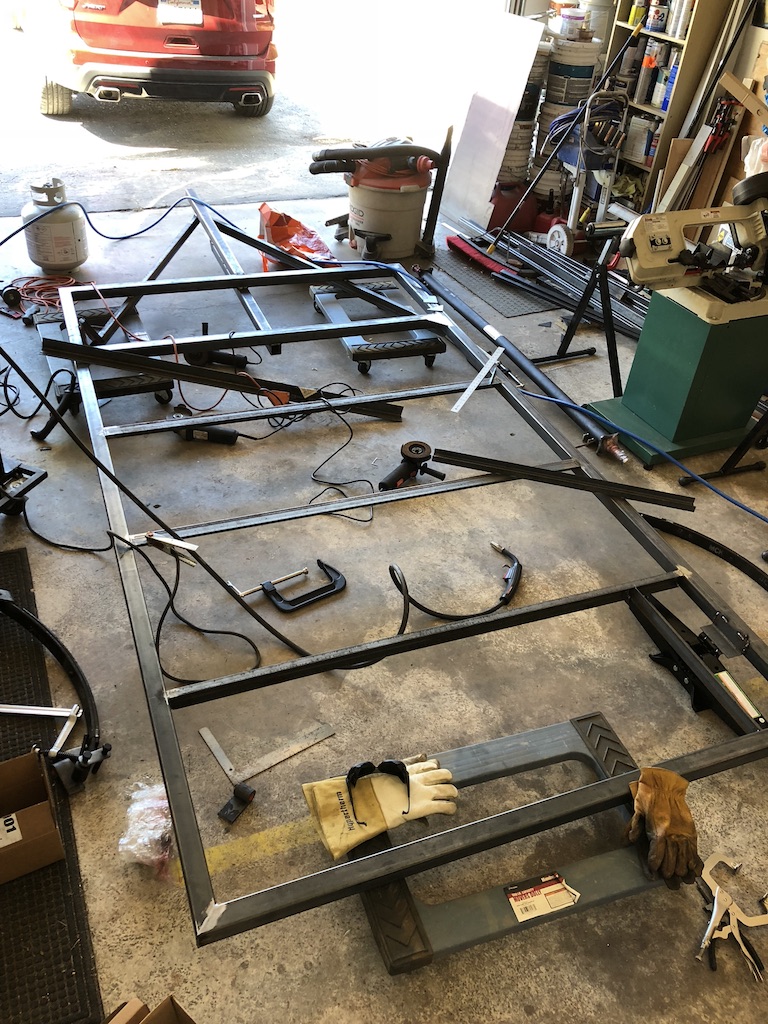
One side complete. Now to make a bracket for the other side.
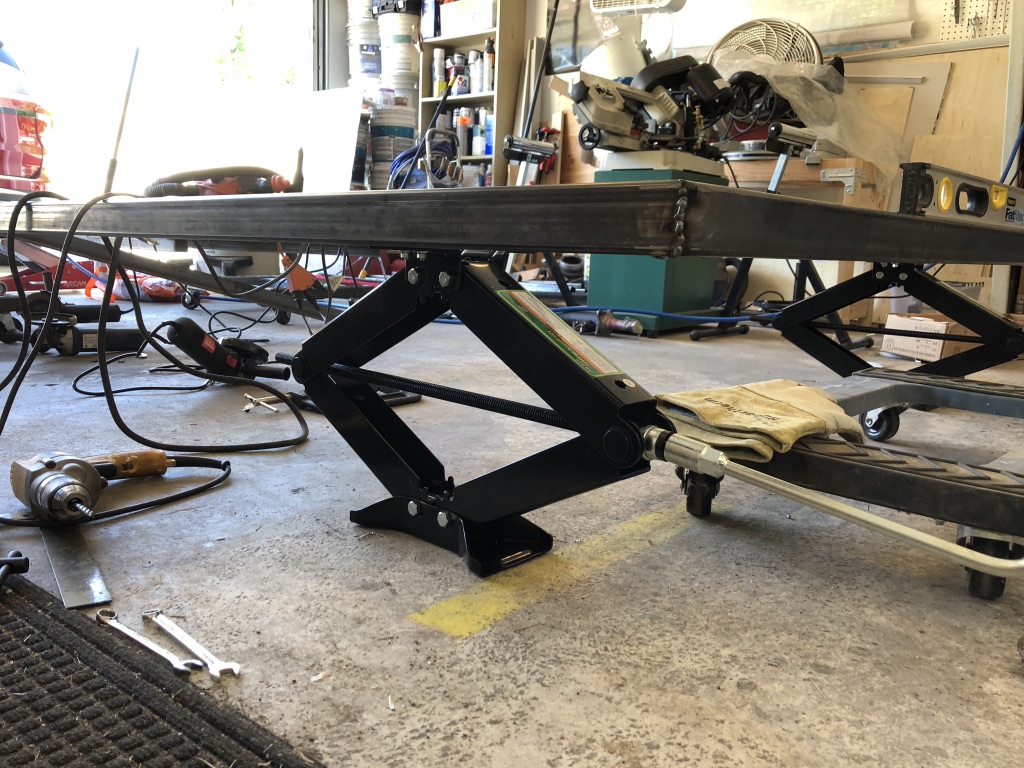
Testing out the jacks.
The jacks were attached to the frame using some bolts so that they can be replaced if needed. Since there was more welding to be completed on the frame, the jacks were used to lift and level the frame for the next bit of the construction.
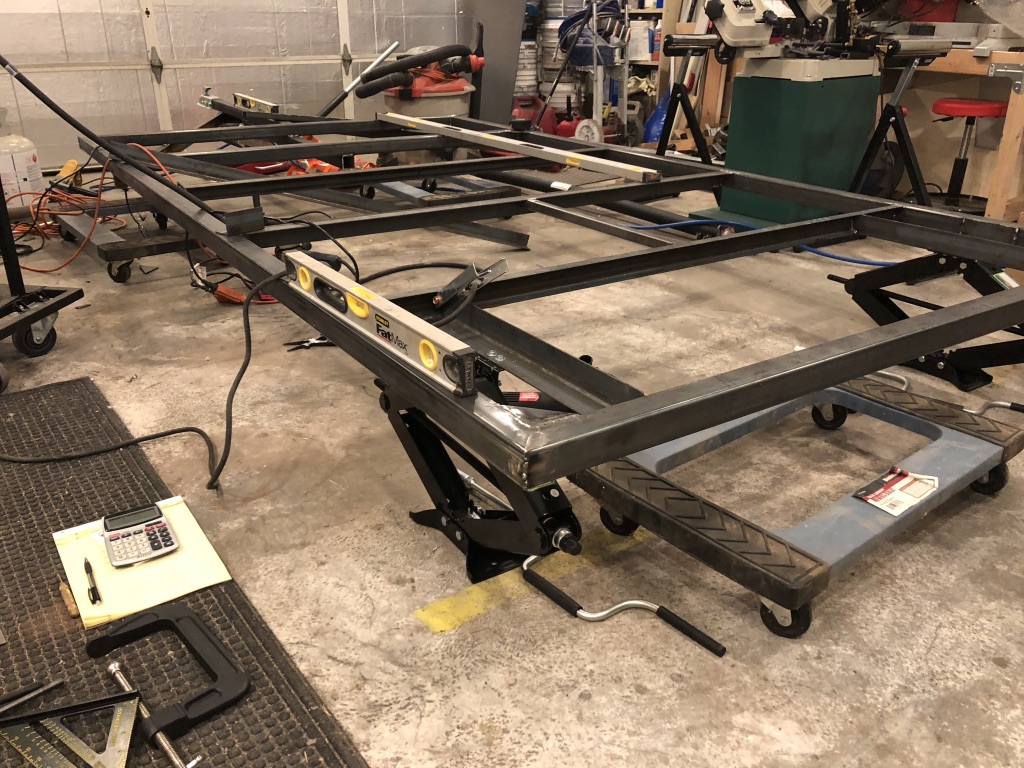
Leveling the whole frame for some more welding.
RV Trailer A-frame construction
2018/06/05 17:49 Filed in: RV Trailer | Welding
Some more cutting of the stock steel, and then some welding, and voila, an a-frame!
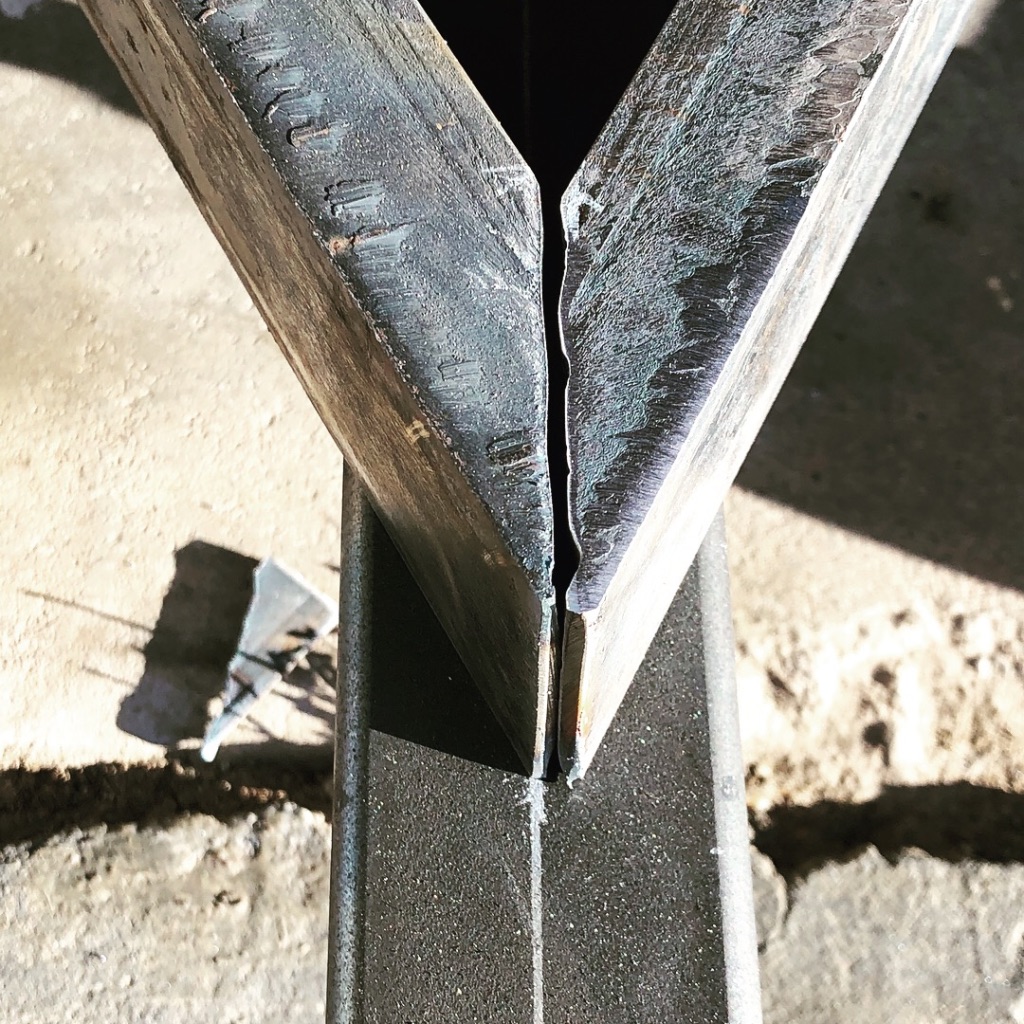
Cutting the stock to form the a-frame
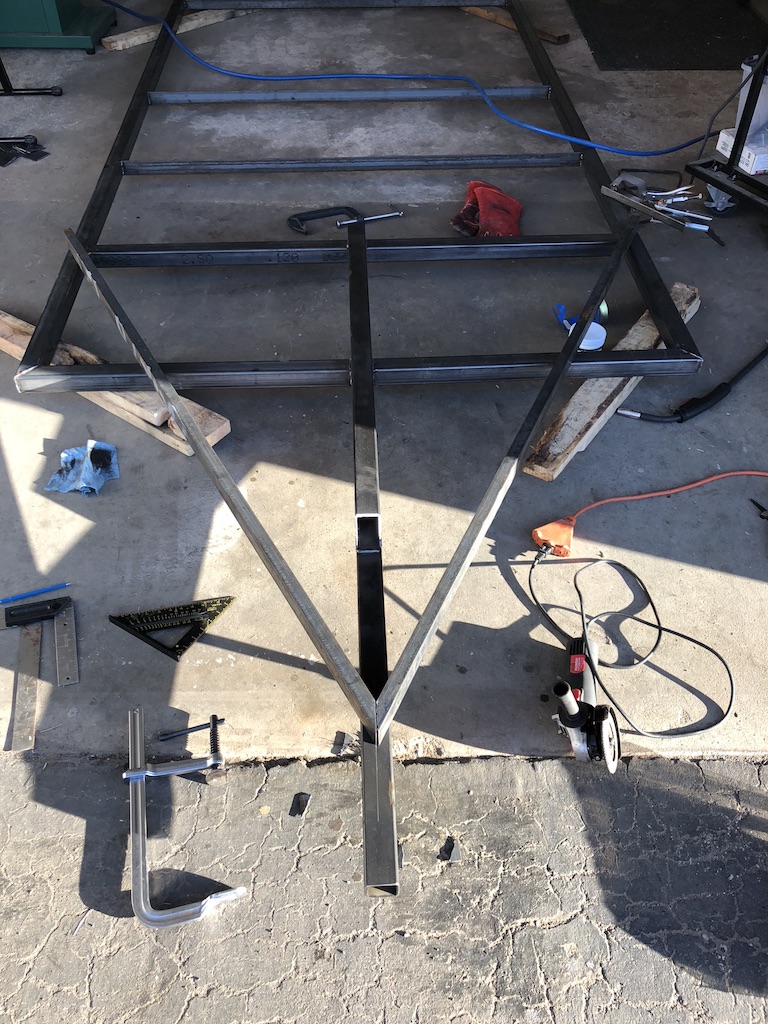
With the c-channel in place, time to weld it together.
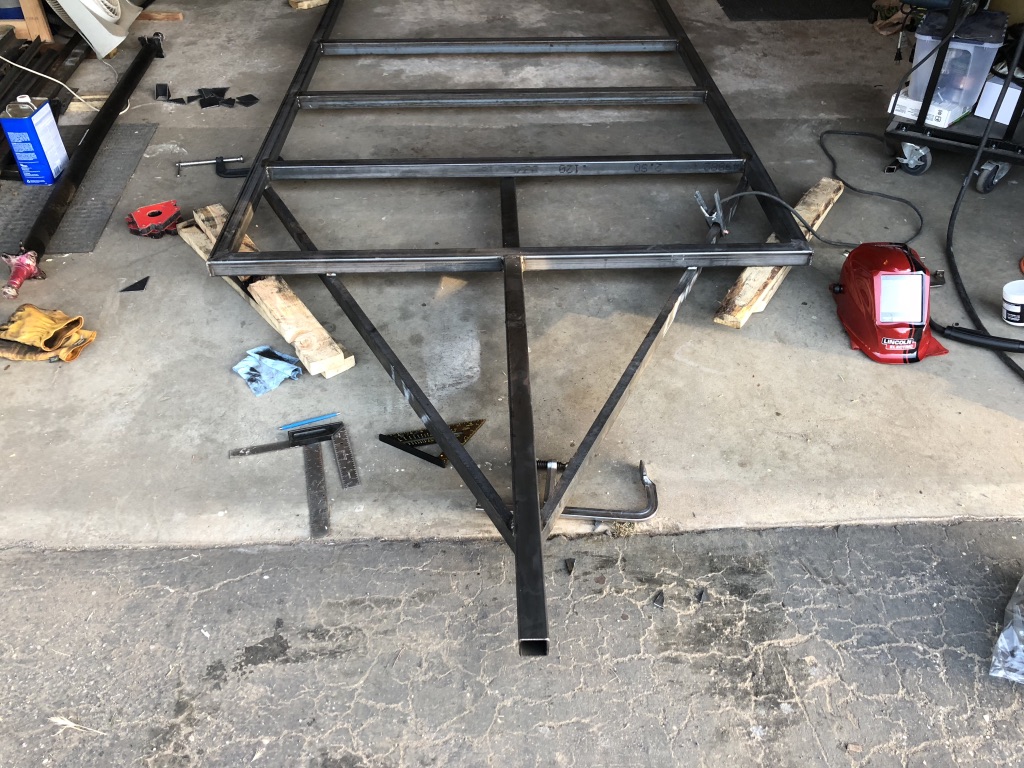
Flip the frame over and weld the other side.
The trailer frame starting to take shape.
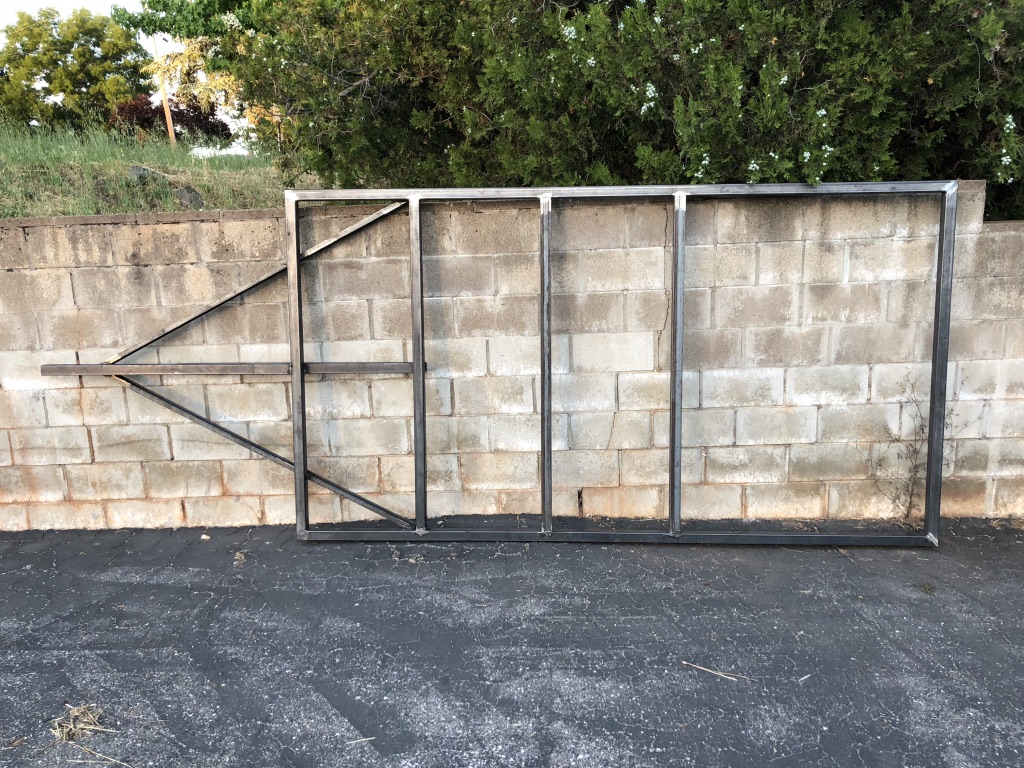
The a-frame welded in place
Receiver bolted on to the frame.
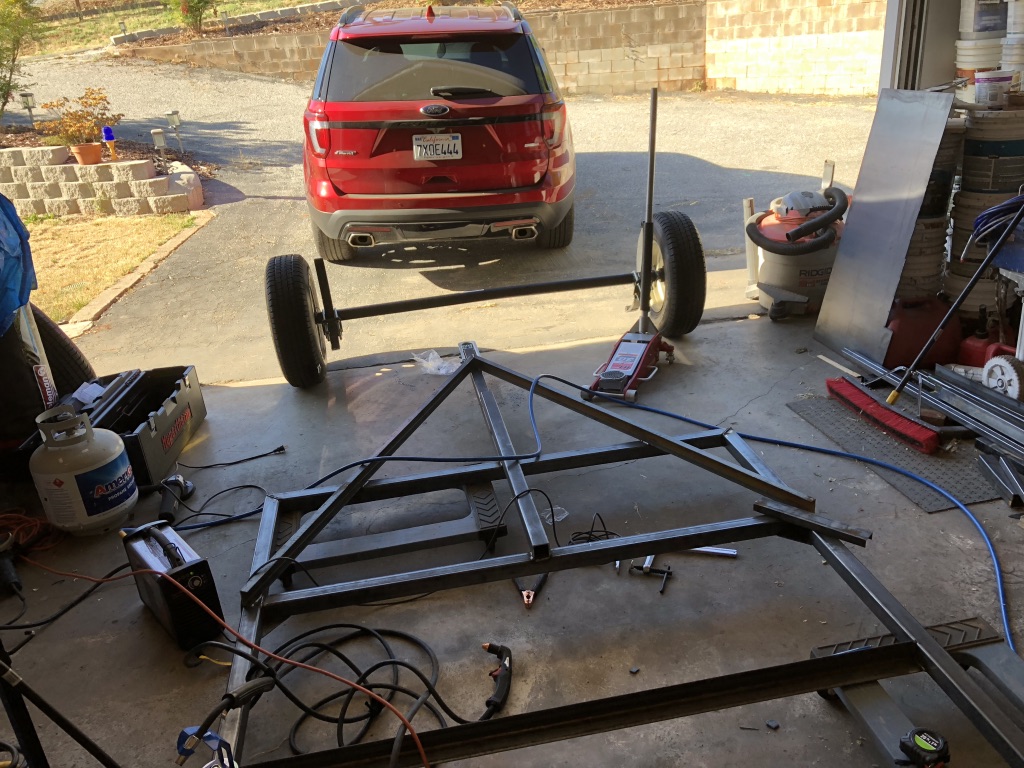
Getting ready for the addition of the axle and the wheels.
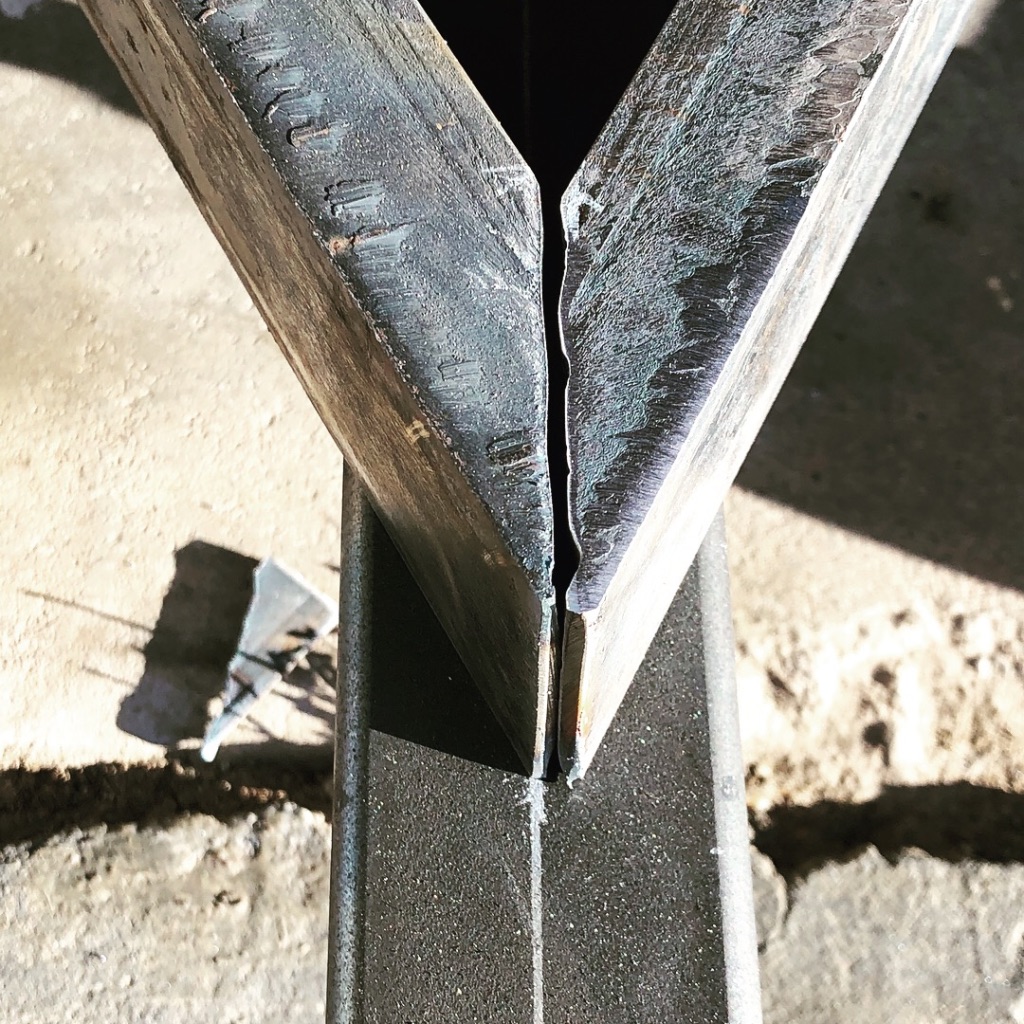
Cutting the stock to form the a-frame
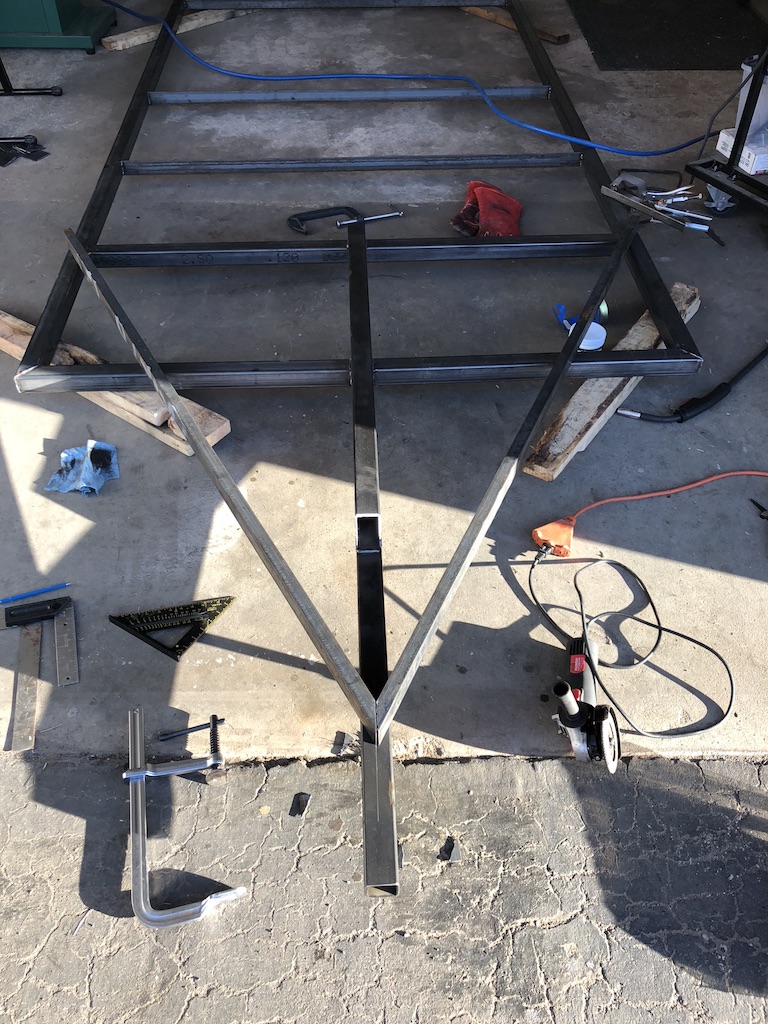
With the c-channel in place, time to weld it together.
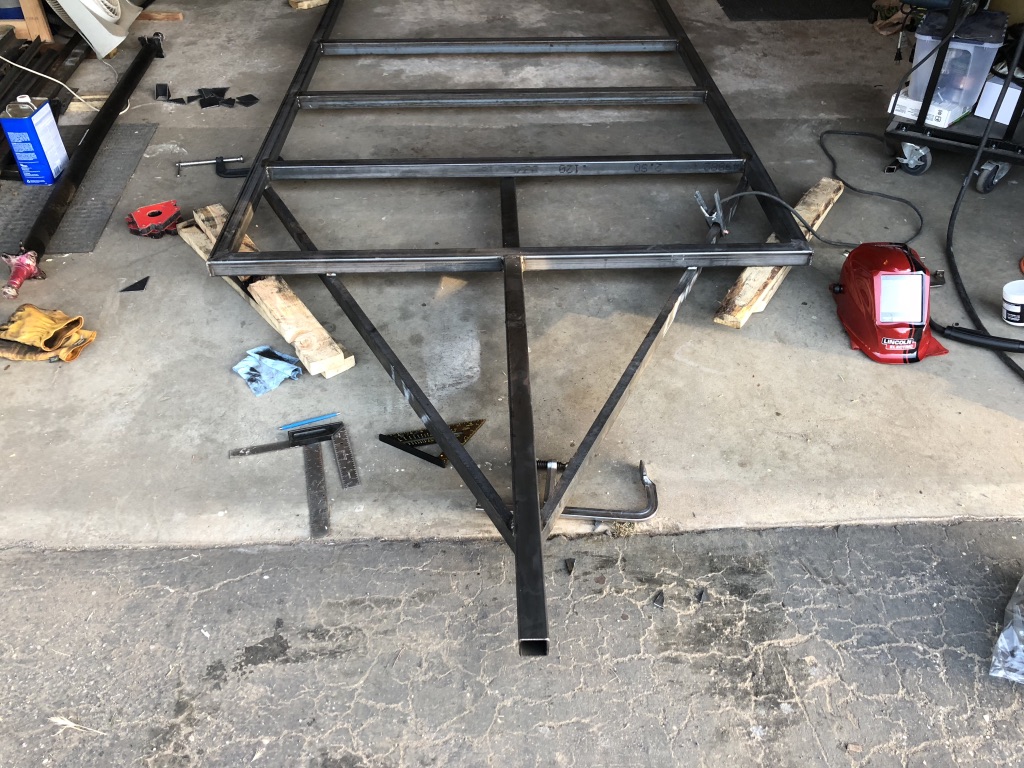
Flip the frame over and weld the other side.
The trailer frame starting to take shape.
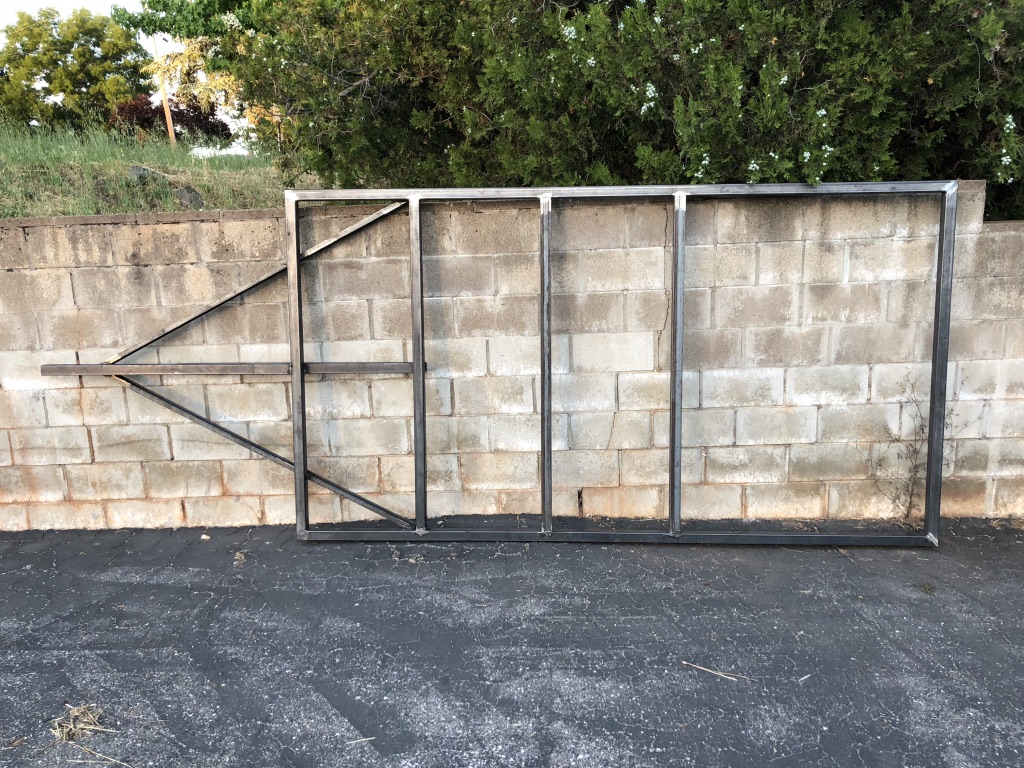
The a-frame welded in place
Receiver bolted on to the frame.
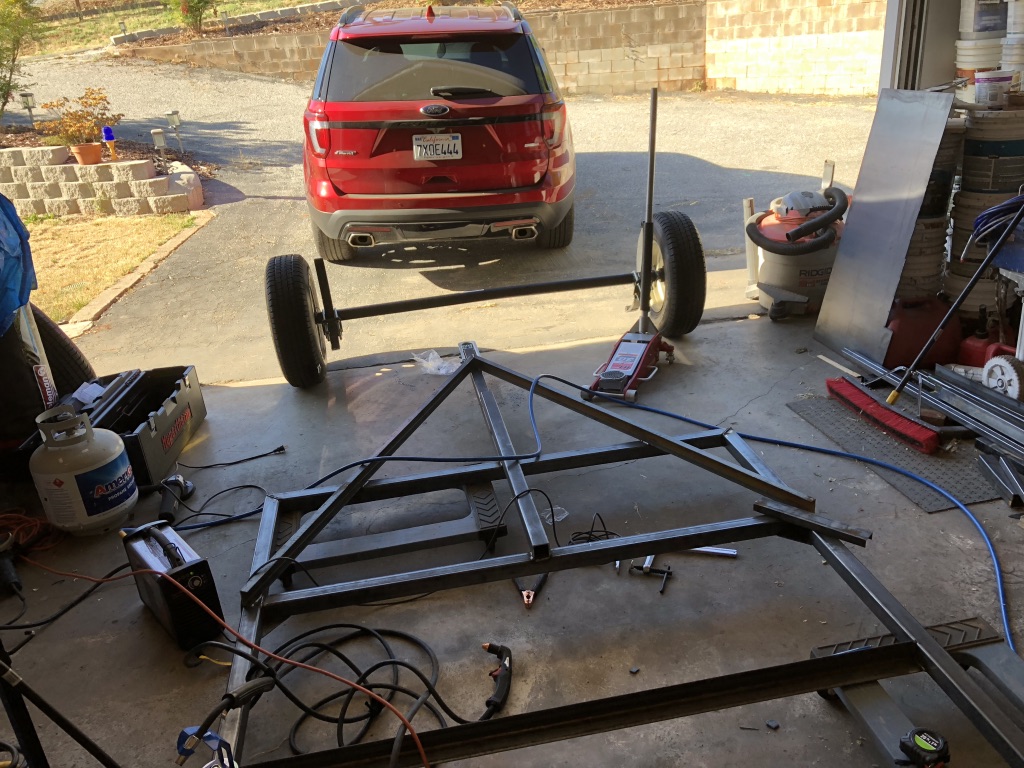
Getting ready for the addition of the axle and the wheels.
The Upgrade
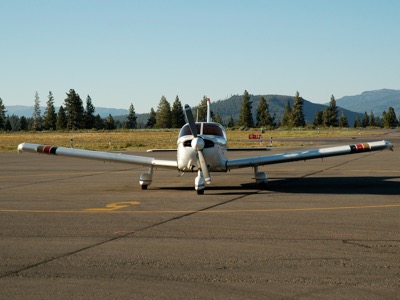
After the engine decided to voice it’s opinion that it needed another cylinder to be replaced, it was time to review my options.
I could replace the latest cylinder, which would then account for 4 out of the 6 cylinders being replaced. However, what would happen next? A trend seems to be forming.
I could replace the remaining 3 cylinders – in essence undertaking (another) top overhaul. Since I did a top-overhaul in late 2004, would this be worth it – trying to milk the engine for more use?
or
I could bite the bullet, and overhaul the engine.
I decided on the last option – time to overhaul the engine!
Well – since the propeller has to have its hub flushed, and possibly overhauled – humm, what about a 3-blader?
So – here goes:
- Engine Overhaul
- Propeller
- Interior….
#5 - it no bang-bang
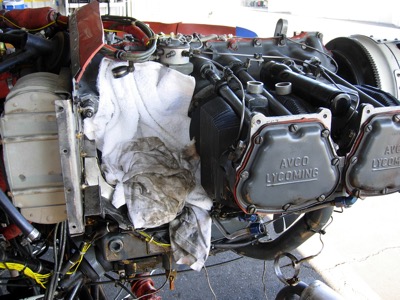
The fun of the Six’s engine started shortly after returning from Oshkosh.
#5 cylinder was not getting producing a good compression test result. After removing the cylinder and sending it out for some work, it was returned overhauled. This was back in September of 2009. The initial flight after the installation of the cylinder was interesting. The run up tests were fine, all six cylinders were behaving normally according to the JPI EDM-700 engine monitor. So, off down the runway, got to take off speed, rotate, and I started to climb. Then #2 cylinder stopped firing (the EDM-700 showed it going cold) and the engine ran rough. Too late to land back on the runway, and the plane was climbing, so a downwind turn was made, and got ready to land back at the airport. Then #2 came alive, and the engine ran smooth.
For some confidence, I continued to fly the plane around the airport for the next 45 minutes – and during the whole time, all six cylinders were firing fine – all looked normal.
Then in early 2010, after chasing an oil leak and trying to determine why cylinder #2 was running rough at low RPM, I gave the keys and a credit card to the local FBO.
The problem was found – #2 and #3 needed to be replaced as well. Michael, the mechanic, did clearly state that swapping out these two cylinders are a gamble, and that there may be additional problems and that I should consider a new overhauled engine.
After coming up with a plan to change the oil at 25 hour intervals, and use an oil analysis service, the two additional cylinders were swapped.